Why do BLDC motor (1 kW) controllers have so many MOSFETs?
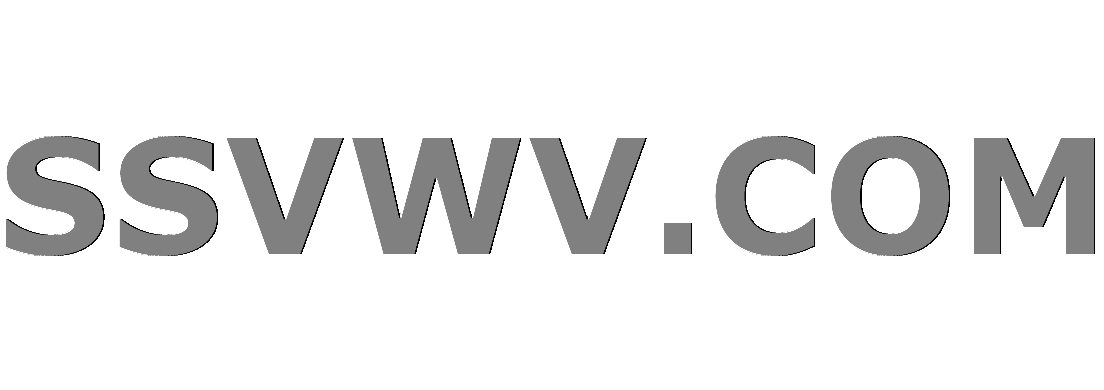
Multi tool use
$begingroup$
I have a 1 kW three-phase BLDC motor from China, and I was developing the controller myself. At 48 Vdc, the maximum current should be about 25 Amps and a peak current of 50 Amps for short durations.
However when I researched BLDC motor controllers, I came across 24-device MOSFET controllers which have four IRFB3607 MOSFETs per phase (4 x 6 = 24).
The IRFB3607 has an Id of 82 Amps at 25 °C and 56 Amps at 100 C. I can't figure out why controllers will be designed with four times the rated current. Keep in mind that these are cheap Chinese controllers.
Any ideas?
mosfet brushless-dc-motor heat switching
New contributor
Sujoy Bhattacharya is a new contributor to this site. Take care in asking for clarification, commenting, and answering.
Check out our Code of Conduct.
$endgroup$
add a comment |
$begingroup$
I have a 1 kW three-phase BLDC motor from China, and I was developing the controller myself. At 48 Vdc, the maximum current should be about 25 Amps and a peak current of 50 Amps for short durations.
However when I researched BLDC motor controllers, I came across 24-device MOSFET controllers which have four IRFB3607 MOSFETs per phase (4 x 6 = 24).
The IRFB3607 has an Id of 82 Amps at 25 °C and 56 Amps at 100 C. I can't figure out why controllers will be designed with four times the rated current. Keep in mind that these are cheap Chinese controllers.
Any ideas?
mosfet brushless-dc-motor heat switching
New contributor
Sujoy Bhattacharya is a new contributor to this site. Take care in asking for clarification, commenting, and answering.
Check out our Code of Conduct.
$endgroup$
3
$begingroup$
You should include a link to an example of mentioned BLDC controller.
$endgroup$
– Bimpelrekkie
17 hours ago
2
$begingroup$
Mosfets in parallel will reduce the effective Rds_on. Lower power dissipation in the controller and better efficiency.
$endgroup$
– Peter Karlsen
16 hours ago
3
$begingroup$
"24 tube Mosfet controllers" Tube?
$endgroup$
– winny
16 hours ago
$begingroup$
Stall current is also likely to be about 10x rated current or about 250A. 4 * 82A per phase sounds quite reasonable.
$endgroup$
– Brian Drummond
6 hours ago
$begingroup$
Consider how many MOSFETs are on a typical PC motherboard VRM. A high-end desktop board designed to cope with a heavily-overclocked 16+ core processor pulling upwards of 500W will have eight high-end MOSFETs at minimum, and possibly 12 to 16. When you look at it this way, a motor that can pull nearly 1 kW continuously needs similarly beefy power delivery.
$endgroup$
– bwDraco
1 hour ago
add a comment |
$begingroup$
I have a 1 kW three-phase BLDC motor from China, and I was developing the controller myself. At 48 Vdc, the maximum current should be about 25 Amps and a peak current of 50 Amps for short durations.
However when I researched BLDC motor controllers, I came across 24-device MOSFET controllers which have four IRFB3607 MOSFETs per phase (4 x 6 = 24).
The IRFB3607 has an Id of 82 Amps at 25 °C and 56 Amps at 100 C. I can't figure out why controllers will be designed with four times the rated current. Keep in mind that these are cheap Chinese controllers.
Any ideas?
mosfet brushless-dc-motor heat switching
New contributor
Sujoy Bhattacharya is a new contributor to this site. Take care in asking for clarification, commenting, and answering.
Check out our Code of Conduct.
$endgroup$
I have a 1 kW three-phase BLDC motor from China, and I was developing the controller myself. At 48 Vdc, the maximum current should be about 25 Amps and a peak current of 50 Amps for short durations.
However when I researched BLDC motor controllers, I came across 24-device MOSFET controllers which have four IRFB3607 MOSFETs per phase (4 x 6 = 24).
The IRFB3607 has an Id of 82 Amps at 25 °C and 56 Amps at 100 C. I can't figure out why controllers will be designed with four times the rated current. Keep in mind that these are cheap Chinese controllers.
Any ideas?
mosfet brushless-dc-motor heat switching
mosfet brushless-dc-motor heat switching
New contributor
Sujoy Bhattacharya is a new contributor to this site. Take care in asking for clarification, commenting, and answering.
Check out our Code of Conduct.
New contributor
Sujoy Bhattacharya is a new contributor to this site. Take care in asking for clarification, commenting, and answering.
Check out our Code of Conduct.
edited 34 mins ago
Dwayne Reid
17.9k21948
17.9k21948
New contributor
Sujoy Bhattacharya is a new contributor to this site. Take care in asking for clarification, commenting, and answering.
Check out our Code of Conduct.
asked 17 hours ago


Sujoy BhattacharyaSujoy Bhattacharya
613
613
New contributor
Sujoy Bhattacharya is a new contributor to this site. Take care in asking for clarification, commenting, and answering.
Check out our Code of Conduct.
New contributor
Sujoy Bhattacharya is a new contributor to this site. Take care in asking for clarification, commenting, and answering.
Check out our Code of Conduct.
Sujoy Bhattacharya is a new contributor to this site. Take care in asking for clarification, commenting, and answering.
Check out our Code of Conduct.
3
$begingroup$
You should include a link to an example of mentioned BLDC controller.
$endgroup$
– Bimpelrekkie
17 hours ago
2
$begingroup$
Mosfets in parallel will reduce the effective Rds_on. Lower power dissipation in the controller and better efficiency.
$endgroup$
– Peter Karlsen
16 hours ago
3
$begingroup$
"24 tube Mosfet controllers" Tube?
$endgroup$
– winny
16 hours ago
$begingroup$
Stall current is also likely to be about 10x rated current or about 250A. 4 * 82A per phase sounds quite reasonable.
$endgroup$
– Brian Drummond
6 hours ago
$begingroup$
Consider how many MOSFETs are on a typical PC motherboard VRM. A high-end desktop board designed to cope with a heavily-overclocked 16+ core processor pulling upwards of 500W will have eight high-end MOSFETs at minimum, and possibly 12 to 16. When you look at it this way, a motor that can pull nearly 1 kW continuously needs similarly beefy power delivery.
$endgroup$
– bwDraco
1 hour ago
add a comment |
3
$begingroup$
You should include a link to an example of mentioned BLDC controller.
$endgroup$
– Bimpelrekkie
17 hours ago
2
$begingroup$
Mosfets in parallel will reduce the effective Rds_on. Lower power dissipation in the controller and better efficiency.
$endgroup$
– Peter Karlsen
16 hours ago
3
$begingroup$
"24 tube Mosfet controllers" Tube?
$endgroup$
– winny
16 hours ago
$begingroup$
Stall current is also likely to be about 10x rated current or about 250A. 4 * 82A per phase sounds quite reasonable.
$endgroup$
– Brian Drummond
6 hours ago
$begingroup$
Consider how many MOSFETs are on a typical PC motherboard VRM. A high-end desktop board designed to cope with a heavily-overclocked 16+ core processor pulling upwards of 500W will have eight high-end MOSFETs at minimum, and possibly 12 to 16. When you look at it this way, a motor that can pull nearly 1 kW continuously needs similarly beefy power delivery.
$endgroup$
– bwDraco
1 hour ago
3
3
$begingroup$
You should include a link to an example of mentioned BLDC controller.
$endgroup$
– Bimpelrekkie
17 hours ago
$begingroup$
You should include a link to an example of mentioned BLDC controller.
$endgroup$
– Bimpelrekkie
17 hours ago
2
2
$begingroup$
Mosfets in parallel will reduce the effective Rds_on. Lower power dissipation in the controller and better efficiency.
$endgroup$
– Peter Karlsen
16 hours ago
$begingroup$
Mosfets in parallel will reduce the effective Rds_on. Lower power dissipation in the controller and better efficiency.
$endgroup$
– Peter Karlsen
16 hours ago
3
3
$begingroup$
"24 tube Mosfet controllers" Tube?
$endgroup$
– winny
16 hours ago
$begingroup$
"24 tube Mosfet controllers" Tube?
$endgroup$
– winny
16 hours ago
$begingroup$
Stall current is also likely to be about 10x rated current or about 250A. 4 * 82A per phase sounds quite reasonable.
$endgroup$
– Brian Drummond
6 hours ago
$begingroup$
Stall current is also likely to be about 10x rated current or about 250A. 4 * 82A per phase sounds quite reasonable.
$endgroup$
– Brian Drummond
6 hours ago
$begingroup$
Consider how many MOSFETs are on a typical PC motherboard VRM. A high-end desktop board designed to cope with a heavily-overclocked 16+ core processor pulling upwards of 500W will have eight high-end MOSFETs at minimum, and possibly 12 to 16. When you look at it this way, a motor that can pull nearly 1 kW continuously needs similarly beefy power delivery.
$endgroup$
– bwDraco
1 hour ago
$begingroup$
Consider how many MOSFETs are on a typical PC motherboard VRM. A high-end desktop board designed to cope with a heavily-overclocked 16+ core processor pulling upwards of 500W will have eight high-end MOSFETs at minimum, and possibly 12 to 16. When you look at it this way, a motor that can pull nearly 1 kW continuously needs similarly beefy power delivery.
$endgroup$
– bwDraco
1 hour ago
add a comment |
2 Answers
2
active
oldest
votes
$begingroup$
The reason to use multiple MOSFETs is to lower power dissipation resulting in a cheaper design.
Yes one MOSFET can handle the current but it will dissipate some power as it does have some resistance, typically 9 mohm for the IRFB3607.
At 25 A that means 25 A * 9 m ohm = 225 mV drop
At 25 A that means 25 A * 225 mV = 5.625 W of power dissipation
A heatsink for that would need to be substantial.
Now let's do the same calculation for 4 IRFB3607 in parallel:
Now 9 mohm is divided by 4 because of 4 parallel devices:
9 m ohm / 4 = 2.25 mohm
At 25 A that means 25 A * 2.25 m ohm = 56.25 mV drop
At 25 A that means 25 A * 56.25 mV = 1.41 W of power dissipation
That 1.41 W is for all MOSFETs together so less than 0.4 W per MOSFET which they can handle easily without any extra cooling.
Above calculation does not take into account that the 9 mohm Rdson will increase when the MOSFETs heat up. That makes the single MOSFET solution even more problematic as an even larger heatsink is required. The 4 MOSFET solution might "just manage" as it still has some margin (the 0.4 W could increase to 1 W and that would still be OK).
If 3 MOSFETs are cheaper than one heatsink (for dissipating 6 Watt) then the 4 MOSFET solution is cheaper.
Also production costs might be slightly lower for placing 4 MOSFETS compared to 1 MOSFET + Heatsink as the MOSFET has to be screwed or clamped to the heatsink, that's manual work so adds cost.
An added benefit is that reliability becomes better as those 4 MOSFETs are by far not "worked" as hard as a the single MOSFET.
Could we use a "4x" bigger, 2.25 mohm MOSFET?
Sure, if you can find it ! 9 mohm is quite low already. It gets increasingly difficult (and more expensive) to get lower as the influence of bonding wires comes into play. Also for sure four "middle of the road" MOSFETs are cheaper than one big fat MOSFET.
$endgroup$
3
$begingroup$
Also a saving on the cost of electricity over the lifetime of the system.
$endgroup$
– Ian Ringrose
14 hours ago
2
$begingroup$
@IanRingrose I doubt the designer cares much about that because they don't pay the electricity bill
$endgroup$
– Chris H
14 hours ago
2
$begingroup$
You also get more passive cooling from having the power dissipated spread over a larger area (4 parts and their required board space)
$endgroup$
– W5VO♦
13 hours ago
5
$begingroup$
@ChrisH but buyer pays electricity bill, and designer cares about his design to sell well. Or at least should care...
$endgroup$
– Mołot
13 hours ago
2
$begingroup$
@ChrisH going "green" and educing carbon footprint is fashionable now, so marketing departments of such companies are more and more interested indeed - even if percentage is quite low, it increases. Similar for private users. Don't have any statistics. From my point of view this trend is visible, even if it's negligible overall.
$endgroup$
– Mołot
12 hours ago
|
show 7 more comments
$begingroup$
For almost all electrical components, lifetime decreases exponentially with increasing temperature. This is especially true with capacitors, which are found in BLDC motor drivers to decrease electrical noise and high-current peaks.
Let's say that the controller with 4 FETs per phase increased in temperature by 10°C at the rated load. Assuming an ambient temperature of 30°C, the controller would be running at 40°C. At this temperature, even standard-temperature range aluminum electrolytic capacitors could last over 120,000 hours.
If the same controller were to be built with 1 FET per phase instead of 4, the resistance would increase by a factor of 4 and the I^2R losses would also increase by the same amount. With the same heat-sink, the controller would experience 4 times the heating above ambient. It would now be running at 70°C. This would cut the lifetime of the capacitors by around a factor of 10, and would also decrease the life of other components similarly. To counteract this, a larger heatsink would be required, and it would be cheaper (and smaller) to just use more FETs.
$endgroup$
add a comment |
Your Answer
StackExchange.ifUsing("editor", function () {
return StackExchange.using("mathjaxEditing", function () {
StackExchange.MarkdownEditor.creationCallbacks.add(function (editor, postfix) {
StackExchange.mathjaxEditing.prepareWmdForMathJax(editor, postfix, [["\$", "\$"]]);
});
});
}, "mathjax-editing");
StackExchange.ifUsing("editor", function () {
return StackExchange.using("schematics", function () {
StackExchange.schematics.init();
});
}, "cicuitlab");
StackExchange.ready(function() {
var channelOptions = {
tags: "".split(" "),
id: "135"
};
initTagRenderer("".split(" "), "".split(" "), channelOptions);
StackExchange.using("externalEditor", function() {
// Have to fire editor after snippets, if snippets enabled
if (StackExchange.settings.snippets.snippetsEnabled) {
StackExchange.using("snippets", function() {
createEditor();
});
}
else {
createEditor();
}
});
function createEditor() {
StackExchange.prepareEditor({
heartbeatType: 'answer',
autoActivateHeartbeat: false,
convertImagesToLinks: false,
noModals: true,
showLowRepImageUploadWarning: true,
reputationToPostImages: null,
bindNavPrevention: true,
postfix: "",
imageUploader: {
brandingHtml: "Powered by u003ca class="icon-imgur-white" href="https://imgur.com/"u003eu003c/au003e",
contentPolicyHtml: "User contributions licensed under u003ca href="https://creativecommons.org/licenses/by-sa/3.0/"u003ecc by-sa 3.0 with attribution requiredu003c/au003e u003ca href="https://stackoverflow.com/legal/content-policy"u003e(content policy)u003c/au003e",
allowUrls: true
},
onDemand: true,
discardSelector: ".discard-answer"
,immediatelyShowMarkdownHelp:true
});
}
});
Sujoy Bhattacharya is a new contributor. Be nice, and check out our Code of Conduct.
Sign up or log in
StackExchange.ready(function () {
StackExchange.helpers.onClickDraftSave('#login-link');
});
Sign up using Google
Sign up using Facebook
Sign up using Email and Password
Post as a guest
Required, but never shown
StackExchange.ready(
function () {
StackExchange.openid.initPostLogin('.new-post-login', 'https%3a%2f%2felectronics.stackexchange.com%2fquestions%2f423363%2fwhy-do-bldc-motor-1-kw-controllers-have-so-many-mosfets%23new-answer', 'question_page');
}
);
Post as a guest
Required, but never shown
2 Answers
2
active
oldest
votes
2 Answers
2
active
oldest
votes
active
oldest
votes
active
oldest
votes
$begingroup$
The reason to use multiple MOSFETs is to lower power dissipation resulting in a cheaper design.
Yes one MOSFET can handle the current but it will dissipate some power as it does have some resistance, typically 9 mohm for the IRFB3607.
At 25 A that means 25 A * 9 m ohm = 225 mV drop
At 25 A that means 25 A * 225 mV = 5.625 W of power dissipation
A heatsink for that would need to be substantial.
Now let's do the same calculation for 4 IRFB3607 in parallel:
Now 9 mohm is divided by 4 because of 4 parallel devices:
9 m ohm / 4 = 2.25 mohm
At 25 A that means 25 A * 2.25 m ohm = 56.25 mV drop
At 25 A that means 25 A * 56.25 mV = 1.41 W of power dissipation
That 1.41 W is for all MOSFETs together so less than 0.4 W per MOSFET which they can handle easily without any extra cooling.
Above calculation does not take into account that the 9 mohm Rdson will increase when the MOSFETs heat up. That makes the single MOSFET solution even more problematic as an even larger heatsink is required. The 4 MOSFET solution might "just manage" as it still has some margin (the 0.4 W could increase to 1 W and that would still be OK).
If 3 MOSFETs are cheaper than one heatsink (for dissipating 6 Watt) then the 4 MOSFET solution is cheaper.
Also production costs might be slightly lower for placing 4 MOSFETS compared to 1 MOSFET + Heatsink as the MOSFET has to be screwed or clamped to the heatsink, that's manual work so adds cost.
An added benefit is that reliability becomes better as those 4 MOSFETs are by far not "worked" as hard as a the single MOSFET.
Could we use a "4x" bigger, 2.25 mohm MOSFET?
Sure, if you can find it ! 9 mohm is quite low already. It gets increasingly difficult (and more expensive) to get lower as the influence of bonding wires comes into play. Also for sure four "middle of the road" MOSFETs are cheaper than one big fat MOSFET.
$endgroup$
3
$begingroup$
Also a saving on the cost of electricity over the lifetime of the system.
$endgroup$
– Ian Ringrose
14 hours ago
2
$begingroup$
@IanRingrose I doubt the designer cares much about that because they don't pay the electricity bill
$endgroup$
– Chris H
14 hours ago
2
$begingroup$
You also get more passive cooling from having the power dissipated spread over a larger area (4 parts and their required board space)
$endgroup$
– W5VO♦
13 hours ago
5
$begingroup$
@ChrisH but buyer pays electricity bill, and designer cares about his design to sell well. Or at least should care...
$endgroup$
– Mołot
13 hours ago
2
$begingroup$
@ChrisH going "green" and educing carbon footprint is fashionable now, so marketing departments of such companies are more and more interested indeed - even if percentage is quite low, it increases. Similar for private users. Don't have any statistics. From my point of view this trend is visible, even if it's negligible overall.
$endgroup$
– Mołot
12 hours ago
|
show 7 more comments
$begingroup$
The reason to use multiple MOSFETs is to lower power dissipation resulting in a cheaper design.
Yes one MOSFET can handle the current but it will dissipate some power as it does have some resistance, typically 9 mohm for the IRFB3607.
At 25 A that means 25 A * 9 m ohm = 225 mV drop
At 25 A that means 25 A * 225 mV = 5.625 W of power dissipation
A heatsink for that would need to be substantial.
Now let's do the same calculation for 4 IRFB3607 in parallel:
Now 9 mohm is divided by 4 because of 4 parallel devices:
9 m ohm / 4 = 2.25 mohm
At 25 A that means 25 A * 2.25 m ohm = 56.25 mV drop
At 25 A that means 25 A * 56.25 mV = 1.41 W of power dissipation
That 1.41 W is for all MOSFETs together so less than 0.4 W per MOSFET which they can handle easily without any extra cooling.
Above calculation does not take into account that the 9 mohm Rdson will increase when the MOSFETs heat up. That makes the single MOSFET solution even more problematic as an even larger heatsink is required. The 4 MOSFET solution might "just manage" as it still has some margin (the 0.4 W could increase to 1 W and that would still be OK).
If 3 MOSFETs are cheaper than one heatsink (for dissipating 6 Watt) then the 4 MOSFET solution is cheaper.
Also production costs might be slightly lower for placing 4 MOSFETS compared to 1 MOSFET + Heatsink as the MOSFET has to be screwed or clamped to the heatsink, that's manual work so adds cost.
An added benefit is that reliability becomes better as those 4 MOSFETs are by far not "worked" as hard as a the single MOSFET.
Could we use a "4x" bigger, 2.25 mohm MOSFET?
Sure, if you can find it ! 9 mohm is quite low already. It gets increasingly difficult (and more expensive) to get lower as the influence of bonding wires comes into play. Also for sure four "middle of the road" MOSFETs are cheaper than one big fat MOSFET.
$endgroup$
3
$begingroup$
Also a saving on the cost of electricity over the lifetime of the system.
$endgroup$
– Ian Ringrose
14 hours ago
2
$begingroup$
@IanRingrose I doubt the designer cares much about that because they don't pay the electricity bill
$endgroup$
– Chris H
14 hours ago
2
$begingroup$
You also get more passive cooling from having the power dissipated spread over a larger area (4 parts and their required board space)
$endgroup$
– W5VO♦
13 hours ago
5
$begingroup$
@ChrisH but buyer pays electricity bill, and designer cares about his design to sell well. Or at least should care...
$endgroup$
– Mołot
13 hours ago
2
$begingroup$
@ChrisH going "green" and educing carbon footprint is fashionable now, so marketing departments of such companies are more and more interested indeed - even if percentage is quite low, it increases. Similar for private users. Don't have any statistics. From my point of view this trend is visible, even if it's negligible overall.
$endgroup$
– Mołot
12 hours ago
|
show 7 more comments
$begingroup$
The reason to use multiple MOSFETs is to lower power dissipation resulting in a cheaper design.
Yes one MOSFET can handle the current but it will dissipate some power as it does have some resistance, typically 9 mohm for the IRFB3607.
At 25 A that means 25 A * 9 m ohm = 225 mV drop
At 25 A that means 25 A * 225 mV = 5.625 W of power dissipation
A heatsink for that would need to be substantial.
Now let's do the same calculation for 4 IRFB3607 in parallel:
Now 9 mohm is divided by 4 because of 4 parallel devices:
9 m ohm / 4 = 2.25 mohm
At 25 A that means 25 A * 2.25 m ohm = 56.25 mV drop
At 25 A that means 25 A * 56.25 mV = 1.41 W of power dissipation
That 1.41 W is for all MOSFETs together so less than 0.4 W per MOSFET which they can handle easily without any extra cooling.
Above calculation does not take into account that the 9 mohm Rdson will increase when the MOSFETs heat up. That makes the single MOSFET solution even more problematic as an even larger heatsink is required. The 4 MOSFET solution might "just manage" as it still has some margin (the 0.4 W could increase to 1 W and that would still be OK).
If 3 MOSFETs are cheaper than one heatsink (for dissipating 6 Watt) then the 4 MOSFET solution is cheaper.
Also production costs might be slightly lower for placing 4 MOSFETS compared to 1 MOSFET + Heatsink as the MOSFET has to be screwed or clamped to the heatsink, that's manual work so adds cost.
An added benefit is that reliability becomes better as those 4 MOSFETs are by far not "worked" as hard as a the single MOSFET.
Could we use a "4x" bigger, 2.25 mohm MOSFET?
Sure, if you can find it ! 9 mohm is quite low already. It gets increasingly difficult (and more expensive) to get lower as the influence of bonding wires comes into play. Also for sure four "middle of the road" MOSFETs are cheaper than one big fat MOSFET.
$endgroup$
The reason to use multiple MOSFETs is to lower power dissipation resulting in a cheaper design.
Yes one MOSFET can handle the current but it will dissipate some power as it does have some resistance, typically 9 mohm for the IRFB3607.
At 25 A that means 25 A * 9 m ohm = 225 mV drop
At 25 A that means 25 A * 225 mV = 5.625 W of power dissipation
A heatsink for that would need to be substantial.
Now let's do the same calculation for 4 IRFB3607 in parallel:
Now 9 mohm is divided by 4 because of 4 parallel devices:
9 m ohm / 4 = 2.25 mohm
At 25 A that means 25 A * 2.25 m ohm = 56.25 mV drop
At 25 A that means 25 A * 56.25 mV = 1.41 W of power dissipation
That 1.41 W is for all MOSFETs together so less than 0.4 W per MOSFET which they can handle easily without any extra cooling.
Above calculation does not take into account that the 9 mohm Rdson will increase when the MOSFETs heat up. That makes the single MOSFET solution even more problematic as an even larger heatsink is required. The 4 MOSFET solution might "just manage" as it still has some margin (the 0.4 W could increase to 1 W and that would still be OK).
If 3 MOSFETs are cheaper than one heatsink (for dissipating 6 Watt) then the 4 MOSFET solution is cheaper.
Also production costs might be slightly lower for placing 4 MOSFETS compared to 1 MOSFET + Heatsink as the MOSFET has to be screwed or clamped to the heatsink, that's manual work so adds cost.
An added benefit is that reliability becomes better as those 4 MOSFETs are by far not "worked" as hard as a the single MOSFET.
Could we use a "4x" bigger, 2.25 mohm MOSFET?
Sure, if you can find it ! 9 mohm is quite low already. It gets increasingly difficult (and more expensive) to get lower as the influence of bonding wires comes into play. Also for sure four "middle of the road" MOSFETs are cheaper than one big fat MOSFET.
edited 12 hours ago
answered 16 hours ago


BimpelrekkieBimpelrekkie
49.4k241111
49.4k241111
3
$begingroup$
Also a saving on the cost of electricity over the lifetime of the system.
$endgroup$
– Ian Ringrose
14 hours ago
2
$begingroup$
@IanRingrose I doubt the designer cares much about that because they don't pay the electricity bill
$endgroup$
– Chris H
14 hours ago
2
$begingroup$
You also get more passive cooling from having the power dissipated spread over a larger area (4 parts and their required board space)
$endgroup$
– W5VO♦
13 hours ago
5
$begingroup$
@ChrisH but buyer pays electricity bill, and designer cares about his design to sell well. Or at least should care...
$endgroup$
– Mołot
13 hours ago
2
$begingroup$
@ChrisH going "green" and educing carbon footprint is fashionable now, so marketing departments of such companies are more and more interested indeed - even if percentage is quite low, it increases. Similar for private users. Don't have any statistics. From my point of view this trend is visible, even if it's negligible overall.
$endgroup$
– Mołot
12 hours ago
|
show 7 more comments
3
$begingroup$
Also a saving on the cost of electricity over the lifetime of the system.
$endgroup$
– Ian Ringrose
14 hours ago
2
$begingroup$
@IanRingrose I doubt the designer cares much about that because they don't pay the electricity bill
$endgroup$
– Chris H
14 hours ago
2
$begingroup$
You also get more passive cooling from having the power dissipated spread over a larger area (4 parts and their required board space)
$endgroup$
– W5VO♦
13 hours ago
5
$begingroup$
@ChrisH but buyer pays electricity bill, and designer cares about his design to sell well. Or at least should care...
$endgroup$
– Mołot
13 hours ago
2
$begingroup$
@ChrisH going "green" and educing carbon footprint is fashionable now, so marketing departments of such companies are more and more interested indeed - even if percentage is quite low, it increases. Similar for private users. Don't have any statistics. From my point of view this trend is visible, even if it's negligible overall.
$endgroup$
– Mołot
12 hours ago
3
3
$begingroup$
Also a saving on the cost of electricity over the lifetime of the system.
$endgroup$
– Ian Ringrose
14 hours ago
$begingroup$
Also a saving on the cost of electricity over the lifetime of the system.
$endgroup$
– Ian Ringrose
14 hours ago
2
2
$begingroup$
@IanRingrose I doubt the designer cares much about that because they don't pay the electricity bill
$endgroup$
– Chris H
14 hours ago
$begingroup$
@IanRingrose I doubt the designer cares much about that because they don't pay the electricity bill
$endgroup$
– Chris H
14 hours ago
2
2
$begingroup$
You also get more passive cooling from having the power dissipated spread over a larger area (4 parts and their required board space)
$endgroup$
– W5VO♦
13 hours ago
$begingroup$
You also get more passive cooling from having the power dissipated spread over a larger area (4 parts and their required board space)
$endgroup$
– W5VO♦
13 hours ago
5
5
$begingroup$
@ChrisH but buyer pays electricity bill, and designer cares about his design to sell well. Or at least should care...
$endgroup$
– Mołot
13 hours ago
$begingroup$
@ChrisH but buyer pays electricity bill, and designer cares about his design to sell well. Or at least should care...
$endgroup$
– Mołot
13 hours ago
2
2
$begingroup$
@ChrisH going "green" and educing carbon footprint is fashionable now, so marketing departments of such companies are more and more interested indeed - even if percentage is quite low, it increases. Similar for private users. Don't have any statistics. From my point of view this trend is visible, even if it's negligible overall.
$endgroup$
– Mołot
12 hours ago
$begingroup$
@ChrisH going "green" and educing carbon footprint is fashionable now, so marketing departments of such companies are more and more interested indeed - even if percentage is quite low, it increases. Similar for private users. Don't have any statistics. From my point of view this trend is visible, even if it's negligible overall.
$endgroup$
– Mołot
12 hours ago
|
show 7 more comments
$begingroup$
For almost all electrical components, lifetime decreases exponentially with increasing temperature. This is especially true with capacitors, which are found in BLDC motor drivers to decrease electrical noise and high-current peaks.
Let's say that the controller with 4 FETs per phase increased in temperature by 10°C at the rated load. Assuming an ambient temperature of 30°C, the controller would be running at 40°C. At this temperature, even standard-temperature range aluminum electrolytic capacitors could last over 120,000 hours.
If the same controller were to be built with 1 FET per phase instead of 4, the resistance would increase by a factor of 4 and the I^2R losses would also increase by the same amount. With the same heat-sink, the controller would experience 4 times the heating above ambient. It would now be running at 70°C. This would cut the lifetime of the capacitors by around a factor of 10, and would also decrease the life of other components similarly. To counteract this, a larger heatsink would be required, and it would be cheaper (and smaller) to just use more FETs.
$endgroup$
add a comment |
$begingroup$
For almost all electrical components, lifetime decreases exponentially with increasing temperature. This is especially true with capacitors, which are found in BLDC motor drivers to decrease electrical noise and high-current peaks.
Let's say that the controller with 4 FETs per phase increased in temperature by 10°C at the rated load. Assuming an ambient temperature of 30°C, the controller would be running at 40°C. At this temperature, even standard-temperature range aluminum electrolytic capacitors could last over 120,000 hours.
If the same controller were to be built with 1 FET per phase instead of 4, the resistance would increase by a factor of 4 and the I^2R losses would also increase by the same amount. With the same heat-sink, the controller would experience 4 times the heating above ambient. It would now be running at 70°C. This would cut the lifetime of the capacitors by around a factor of 10, and would also decrease the life of other components similarly. To counteract this, a larger heatsink would be required, and it would be cheaper (and smaller) to just use more FETs.
$endgroup$
add a comment |
$begingroup$
For almost all electrical components, lifetime decreases exponentially with increasing temperature. This is especially true with capacitors, which are found in BLDC motor drivers to decrease electrical noise and high-current peaks.
Let's say that the controller with 4 FETs per phase increased in temperature by 10°C at the rated load. Assuming an ambient temperature of 30°C, the controller would be running at 40°C. At this temperature, even standard-temperature range aluminum electrolytic capacitors could last over 120,000 hours.
If the same controller were to be built with 1 FET per phase instead of 4, the resistance would increase by a factor of 4 and the I^2R losses would also increase by the same amount. With the same heat-sink, the controller would experience 4 times the heating above ambient. It would now be running at 70°C. This would cut the lifetime of the capacitors by around a factor of 10, and would also decrease the life of other components similarly. To counteract this, a larger heatsink would be required, and it would be cheaper (and smaller) to just use more FETs.
$endgroup$
For almost all electrical components, lifetime decreases exponentially with increasing temperature. This is especially true with capacitors, which are found in BLDC motor drivers to decrease electrical noise and high-current peaks.
Let's say that the controller with 4 FETs per phase increased in temperature by 10°C at the rated load. Assuming an ambient temperature of 30°C, the controller would be running at 40°C. At this temperature, even standard-temperature range aluminum electrolytic capacitors could last over 120,000 hours.
If the same controller were to be built with 1 FET per phase instead of 4, the resistance would increase by a factor of 4 and the I^2R losses would also increase by the same amount. With the same heat-sink, the controller would experience 4 times the heating above ambient. It would now be running at 70°C. This would cut the lifetime of the capacitors by around a factor of 10, and would also decrease the life of other components similarly. To counteract this, a larger heatsink would be required, and it would be cheaper (and smaller) to just use more FETs.
answered 2 mins ago
Thor LancasterThor Lancaster
613
613
add a comment |
add a comment |
Sujoy Bhattacharya is a new contributor. Be nice, and check out our Code of Conduct.
Sujoy Bhattacharya is a new contributor. Be nice, and check out our Code of Conduct.
Sujoy Bhattacharya is a new contributor. Be nice, and check out our Code of Conduct.
Sujoy Bhattacharya is a new contributor. Be nice, and check out our Code of Conduct.
Thanks for contributing an answer to Electrical Engineering Stack Exchange!
- Please be sure to answer the question. Provide details and share your research!
But avoid …
- Asking for help, clarification, or responding to other answers.
- Making statements based on opinion; back them up with references or personal experience.
Use MathJax to format equations. MathJax reference.
To learn more, see our tips on writing great answers.
Sign up or log in
StackExchange.ready(function () {
StackExchange.helpers.onClickDraftSave('#login-link');
});
Sign up using Google
Sign up using Facebook
Sign up using Email and Password
Post as a guest
Required, but never shown
StackExchange.ready(
function () {
StackExchange.openid.initPostLogin('.new-post-login', 'https%3a%2f%2felectronics.stackexchange.com%2fquestions%2f423363%2fwhy-do-bldc-motor-1-kw-controllers-have-so-many-mosfets%23new-answer', 'question_page');
}
);
Post as a guest
Required, but never shown
Sign up or log in
StackExchange.ready(function () {
StackExchange.helpers.onClickDraftSave('#login-link');
});
Sign up using Google
Sign up using Facebook
Sign up using Email and Password
Post as a guest
Required, but never shown
Sign up or log in
StackExchange.ready(function () {
StackExchange.helpers.onClickDraftSave('#login-link');
});
Sign up using Google
Sign up using Facebook
Sign up using Email and Password
Post as a guest
Required, but never shown
Sign up or log in
StackExchange.ready(function () {
StackExchange.helpers.onClickDraftSave('#login-link');
});
Sign up using Google
Sign up using Facebook
Sign up using Email and Password
Sign up using Google
Sign up using Facebook
Sign up using Email and Password
Post as a guest
Required, but never shown
Required, but never shown
Required, but never shown
Required, but never shown
Required, but never shown
Required, but never shown
Required, but never shown
Required, but never shown
Required, but never shown
Fn8nrYSc7XLIYOMSWr e,ys51XFFEv9P,y C9WKKkwNp
3
$begingroup$
You should include a link to an example of mentioned BLDC controller.
$endgroup$
– Bimpelrekkie
17 hours ago
2
$begingroup$
Mosfets in parallel will reduce the effective Rds_on. Lower power dissipation in the controller and better efficiency.
$endgroup$
– Peter Karlsen
16 hours ago
3
$begingroup$
"24 tube Mosfet controllers" Tube?
$endgroup$
– winny
16 hours ago
$begingroup$
Stall current is also likely to be about 10x rated current or about 250A. 4 * 82A per phase sounds quite reasonable.
$endgroup$
– Brian Drummond
6 hours ago
$begingroup$
Consider how many MOSFETs are on a typical PC motherboard VRM. A high-end desktop board designed to cope with a heavily-overclocked 16+ core processor pulling upwards of 500W will have eight high-end MOSFETs at minimum, and possibly 12 to 16. When you look at it this way, a motor that can pull nearly 1 kW continuously needs similarly beefy power delivery.
$endgroup$
– bwDraco
1 hour ago